Sensing technologies are widely used to monitor industrial equipment (during operation). But how useful are IoT-related technologies for asset maintenance in commercial buildings? In this article, we’ll look at how sensor data can improve building maintenance effectiveness, from asset monitoring and alerts to smart building predictive maintenance.
Reactive, preventive, and smart building predictive maintenance approaches
Which maintenance approach to choose for your facilities? Non-critical items in a building can run to failure without causing major issues. These are usually also quick and inexpensive to replace (light bulbs, for instance). For more critical assets, money spent on preventive maintenance will almost always be less than the costs you incur due to actual failures, unplanned downtime, and corrective interventions. For building components that are not very susceptible to sudden, unforeseen breakdowns, preventive, planned maintenance, is an adequate strategy. Preventive maintenance intervals are time- or usage-based, and the optimal maintenance frequency is determined using standards, experience, and instructions from equipment manufacturers. Planned maintenance tries to strike a balance between too much maintenance (excessive cost) and too little maintenance (downtime, bad SLA) based on ‘average’ performance.
Predictive maintenance takes this a step further by accurately predicting when equipment failure is likely to occur and aligning maintenance tasks to be performed before it occurs. Such a strategy is designed to predict failures before they happen – allowing time for remedial action without disrupting workflows while at the same time extending the lifecycle of the equipment.
It must be said, however, that each approach has its benefits and limitations. For example, setting up predictive maintenance requires specialist knowledge – this is not always worth the effort. Organizations are, therefore, advised to adopt different maintenance strategies depending on their activities (e.g., office buildings, warehouses, health care facilities, transport infrastructure, power plants), the type of assets, and their criticality to their business.
With global warming an increasingly pressing problem, building maintenance and equipment replacement should also be seen as an opportunity to increase environmental sustainability and accelerate the energy transition.
Problem detection and alerts
“Management by walking around” may sound sympathetic, but in the case of building management, it’s a bad idea, especially if your portfolio includes several buildings or sites. In that case, continuous monitoring and sensor data will become almost indispensable to quickly alert the FM team to anomalies and prevent or minimize failures. Connected sensors that monitor different parameters (temperature, humidity, CO2, VOCs, air pressure, energy consumption, vibrations due to moving parts, etc.) provide indications of malfunctioning systems, such as clogged air filters in HVAC systems, a defective circulation pump, or leaks.
Automated follow-up through workflow-based software
Problem detection is the first step, the next one is to make incoming alerts actionable. With workflow-based software, you can set up automatic processes using an ‘if this then that’ logic, converting alerts into work orders and assigning them to the internal FM team or external maintenance parties. For example, if a set temperature threshold in the server room is exceeded, a work order is sent out to check the HVAC. Or when sensors pick up a malfunction of a loading dock gate in a warehouse, a work order is dispatched to fix the issue. This process can be highly automated so that suppliers receive an overview of work to be carried out – often before users are even aware of a potential problem.
Read more about the role of specialized maintenance software:
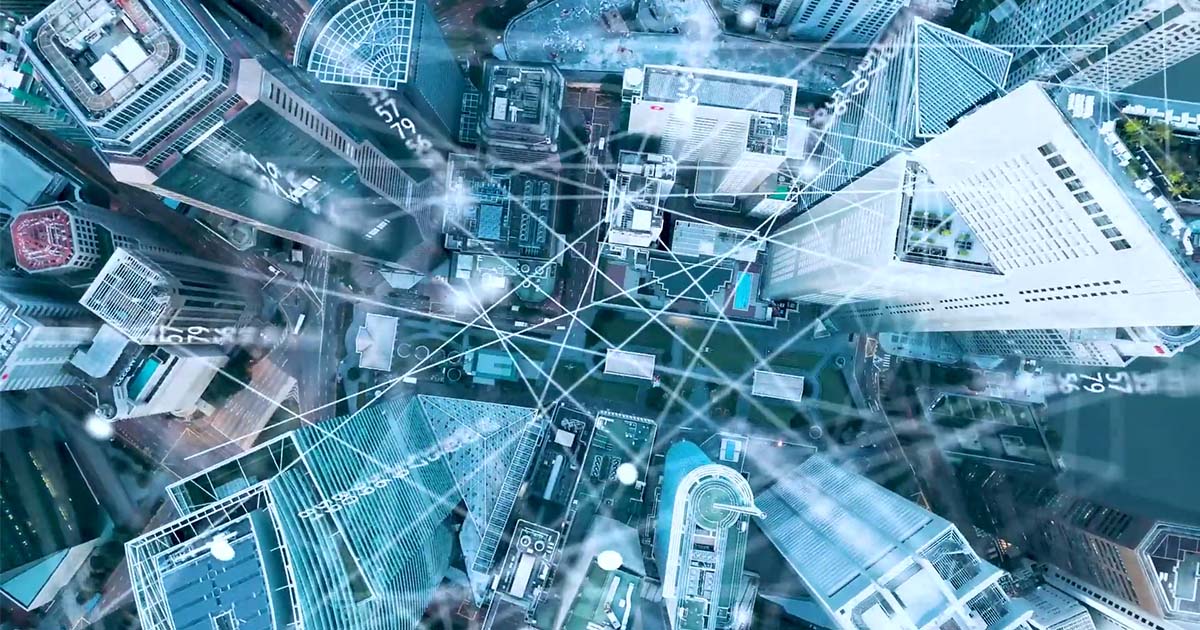
Smart building predictive maintenance
Predictive maintenance is condition-based. It doesn’t rely on fixed time intervals or usage frequency to determine when maintenance is due. Smart building predictive maintenance uses continual monitoring, fault detection, and machine learning to decide if equipment failure is likely to occur. When a fault is developing, sensors pick this up, so that maintenance can be performed only when needed, saving on unnecessary costs. This approach is also likely to prevent (irreversible) damage to an asset.
The learning process is based on (third-party) fault detection models. These determine and show the normal behavior of an asset. If the incoming data indicates that there is a deviation from this normal pattern, there will be fault detection. The Machine Learning Engine will interpret models and ensure that action is taken (e.g., the asset is used more intensively than expected, so the maintenance must be scheduled earlier). By influencing setting points, the preventive plan becomes a predictive maintenance plan, with timely interventions and smart scheduling. The foundation for this is your CMMS/IWMS software integrating your assets, spaces, processes, people, and maintenance planning.
Don’t hesitate to contact us to explore how smart maintenance supported by IoT can benefit your building management.