More and more companies are using preventive maintenance because it enables them both to optimize the work of maintenance teams and improve the productivity of the organization in general. Even if it does not render curative maintenance obsolete, it has become an essential tool enhancing the competitiveness of any company with maintenance activities.
Although the principles of preventive maintenance were developed before the arrival of the first CMMS (Computerised maintenance management system) software, this has enabled companies to make it systematic and much more efficient. Today, CMMS has become essential in applying a relevant preventive maintenance plan.
What is preventive maintenance?
Preventive maintenance is an elaborate maintenance strategy that enables you to optimize the productivity of maintenance work on equipment.
From curative maintenance to preventive maintenance
For a long time, the work of maintenance technicians mainly consisted in repairing defective equipment, either temporarily or permanently. This is what is commonly referred to as curative maintenance. This strategy is the easiest to apply, because it does not require either specific computer tools or the implementation of an elaborate maintenance plan, even if these measures may help make it more efficient. This is why it is still very widespread today, in particular among SMEs.
Definition and objectives of preventive maintenance
A preventive maintenance strategy consists in putting in place different actions whose aim is to reduce the risks of equipment malfunctioning before it happens. Research and technology organization TWI defines it as the “regular and routine maintenance of equipment and assets in order to keep them running and prevent any costly unplanned downtime from unexpected equipment failure.”
Preventive maintenance has three main baselines:
- regulatory provisions, which require periodical checks on certain assets,
- manufacturer recommendations, which must be observed so that the warranty or quality assurance is applied if necessary,
- observation of assets’ operation and user feedback.
The two main objectives of preventive maintenance are to extend the life cycle of assets and optimize productivity by avoiding unexpected stoppages in production or use. It also:
- reduces the duration of work,
- improves the conditions of execution of curative or corrective maintenance actions,
- prevents abnormal energy consumption,
- improves the working conditions of maintenance teams and all staff,
- reduces the causes of serious accidents,
- reduces the cost of maintenance.
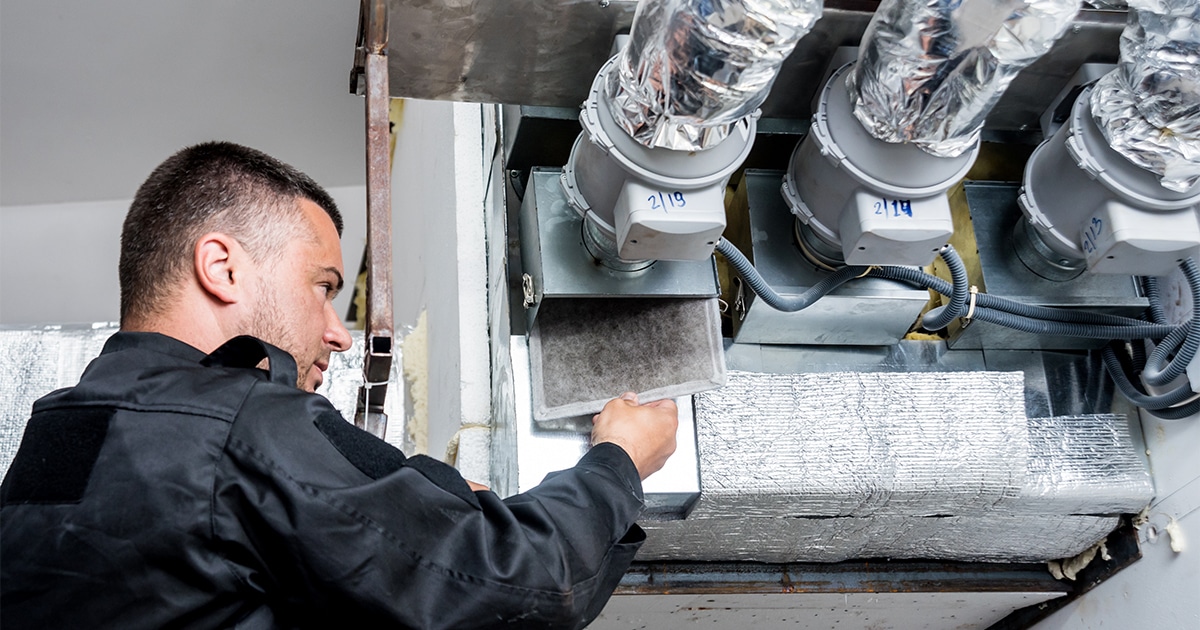
The 3 types of preventive maintenance
There are three main types of preventive maintenance, each corresponding to a level of complexity and efficiency.
Systematic maintenance
Systematic maintenance consists in carrying out maintenance operations on an asset at regular intervals, which are often determined according to a time unit. It is therefore carried out without taking into account the actual status of the equipment concerned.
In general, this strategy is applied to assets that are subject to regulations requiring regular work, or equipment whose failures have a particularly high cost or may lead to serious accidents.
Conditional maintenance
Conditional maintenance is based on the monitoring of an asset or item of equipment’s operation and certain parameters that are applied to it (energy consumption, pressure, etc.). Depending on the observations made, maintenance work is planned and carried out to avoid the appearance of malfunctions.
This strategy mitigates the disadvantages of systematic maintenance, which does not take into account asset monitoring. It may involve permanently recording parameters, or measuring them periodically.
Predictive maintenance
Predictive maintenance is a form of preventive maintenance which relies on the asset’s operating and deterioration parameters and the predictions extrapolated from their analysis. The implementation of this type of strategy aims to only perform the necessary maintenance work while preventing asset breakdowns, malfunctions, or deterioration.
Predictive maintenance requires permanent observation of the equipment concerned and the use of suitable IT tools. CMMS and the arrival of connected sensors have therefore been a great step forward for its distribution across a large number of business sectors.
Why adopt a preventive maintenance plan?
The implementation of a preventive maintenance plan has several advantages in comparison to curative maintenance:
- the extension of building and equipment life cycles,
- improved safety for users,
- reduced frequency and duration of maintenance work periods requiring the immobilization of equipment and buildings.
Ultimately, the company’s overall productivity benefits from the adoption of a preventive maintenance plan. But for this to be simple and fully effective, it requires the use of suitable tools, and therefore a CMMS.
CMMS improving preventive maintenance
To put in place a preventive maintenance strategy, it is virtually essential to have efficient CMMS software. With this software, the operating parameters of the assets to be maintained can be analyzed and preventive maintenance work planned.
Preparing for preventive maintenance
Before putting in place a preventive maintenance plan, you must first determine this plan’s scope of application. Then, you need to choose the maintenance level to apply: systematic, conditional, or predictive. Finally, you must use CMMS software that is suitable for the company’s business sector and implement a preventive maintenance plan.
The benefits of CMMS
To adopt preventive maintenance for a building, certain steps are essential. You must draw up an exhaustive inventory of the assets (structural and architectural, specialist equipment, etc.), prioritize these assets, then determine their criticality. This is determined based on the operational risks related to the organization’s purpose, and the probability of failure.
To this end, a BIM plan may be an excellent tool to facilitate the creation of a building’s full inventory.
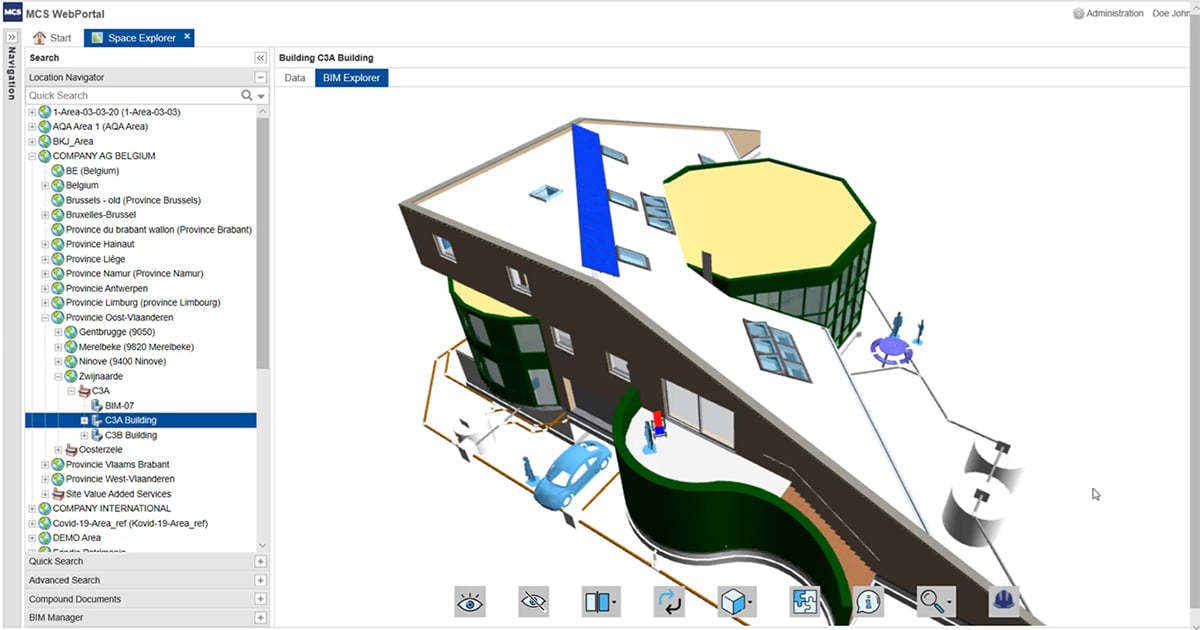
It is only possible to carry out these actions with an efficient CMMS, whose functions are suitable for the implementation of a preventive maintenance strategy.
How to create a preventive maintenance plan with CMMS software
By using suitable CMMS software, preventive maintenance can easily be put in place. For example, a systematic calendar-type preventive maintenance plan will be established following these different steps:
- selecting a type of event to create,
- choosing its frequency,
- choosing the number of repetitions,
- selecting the equipment families,
- selecting the maintenance technicians involved,
- choosing a due date,
- defining the material conditions for maintenance work,
- defining the duration of work,
- adding the necessary documentation.
To create a conditional or predictive maintenance plan, it will be necessary to integrate sensors, or other tools to observe equipment operation, in the CMMS software used.
Transitioning from preventive to predictive maintenance
Predictive maintenance is the most developed form of preventive maintenance. Carrying out continuous monitoring of the status of an asset or installation enables you to perform maintenance work ‘just in time’, i.e. neither too early nor too late. The maintenance costs are therefore reduced to a minimum, most failures are avoided, and curative maintenance actions, which may be costly, are also avoided.
To set it up, it is essential to use a suitable CMMS. For example, a predictive preventive maintenance plan can plan work when a previously defined maximum operating temperature is reached on an installation. In this case, the CMMS software automatically generates a maintenance operation to avoid failure.
The CMMS is the only tool capable of gathering the data sent by the sensors on the equipment, analyzing it, and using it within the framework of a preventive maintenance plan.
Preventive maintenance developed strongly with the arrival of CMMS software. It has also been perfected, taking the equipment’s actual and observed operation into account more and more, and not only its presumed maintenance needs. However, its efficiency depends both on the solution chosen and the type of strategy applied.
By adopting powerful CMMS software that is adapted to the most innovative methods, not only do companies optimize their maintenance activities, but they also prepare to incorporate the latest technological advancements such as connected sensors, through which the most efficient form of maintenance – predictive maintenance – becomes possible. They, therefore, give themselves the means to remain competitive in the long term.
Frequently asked questions
The use of CMMS software is the most suitable solution to revitalize preventive maintenance, as it greatly facilitates real-time monitoring of your installations.
Thanks to CMMS, you can move towards predictive maintenance by continuously monitoring your installations. Predictive maintenance ensures that you are there at the right time.